
Volvo Safety Center
By Larkin Hill
In Latin Volvo means "I roll." The circle and arrow badge found on the grille was derived from a symbol for iron ore and represents strength. Together they suggest rolling strength -- something that Assar Gabrielsson and Gustaf Larson saw a distinct need for in the automotive market.
![]() |
|
Armed with extensive automotive industry experience and frustrated with the quality of vehicles being produced around the world, Assar Gabrielsson and Gustaf Larson joined together to build safe, reliable, and high-quality vehicles for their home country of Sweden. With the right connections, and a quest to provide Innovation, Quality, and Commitment to the people, the first Volvo car was born in 1927. | |
In 1924, employing their native country's high quality steel, the two Swedish gentlemen decided to design and manufacture a vehicle that would be able to withstand the rigors of their country's harsh winter conditions. However, a high-endurance vehicle was only one element of the plan.
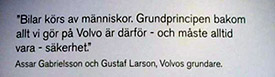

The words are simple and the meaning is plain, and Volvo has kept with its human commitment ever since it's first vehicle introduction in 1927. In fact, when the first Volvo rolled off the assembly line, it was vehicle in the world that was equipped with automatic windshield wipers and safety glass.
Volvo was also the first to use a safety steel cage ('44), laminated windshield ('44), padded instrument panel ('60), electronic rear-window defroster ('73), ABS brakes ('84), build-in booster seat ('91), and side-impact air bags ('94). However, Volvo is most well known for their invention of the three-point safety belt, which was patented in 1958 and introduced on vehicles in 1959
In 1966, a survey of all Volvo accidents in Sweden was conducted and the results suggested that the three-point seat belt had reduced injuries by approximately 50%. With this discovery, Volvo realized the value of real world crash knowledge for future design and in 1972 Volvo's Traffic Accident Research team was officially formed. However, while the Accident Research Team has been able to able to study more than 45,000 collisions in the real-world environment, they were still confined to the traditional front and side crashed within the laboratory.
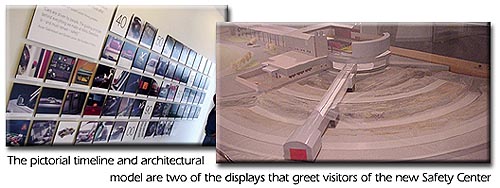
Continuing their commitment to the advancements in safety technology, Volvo has built the most comprehensive crash safety laboratory in the world. Opening its doors on April 2000, the new $81 billion was designed to provide the most realistic collision environment possible.



This fall, Volvo opened its doors to the media and demonstrated the facilities capabilities by organizing a crash between an S80 and a V40.
"Knowledge saves lives!" The statement is simple and can be applied to almost anything -- Volvo has been using it for years. However, Christor Gustafsson, Senior Safety Engineer, embellished the declaration with the statement that "Knowledge is important - but what you do with knowledge is most important." And that's why Volvo has invested its time, money and commitment to building a facility capable of simulating real-life accidents in a controlled environment.
![]() |
|
The first of its kind, the new high-tech crash barrier is fitted with piezo-electric sensors that measure the impact from both the front and the side of a corner. Meaning, as the vehicle is "wrapped around" an angle, sensors read the vehicle's reaction from all angles. In addition, twelve compressed air cushions located beneath the block enable the barrier to be moved to accommodate any angle desired for testing. | |
In the past, most crash tests fell into three basic accident types (side, front, and rear), however, the new facility's 90-degree moveable arm will enable numerous other variations to be performed. The most beneficial testing capabilities will include various offset head-on collisions, as they are the most common and most difficult to accurately simulate. At speeds as high as 125 kilometers per hour, or 75 miles per hour for cars, the moveable arm can be adjusted to any position within a 180 and 90-degree angle. Thus the engineers will be able to test any combination of vehicles at a large variety of speeds, creating virtually endless combinations. In addition, various faux inanimate objects, such as lampposts, roadside barriers, truck platforms, and animals, will be used for testing.
![]() |
|
The new safety center will enable engineers to test and study the reactions of the various Volvo's, when a large moveable object is hit at high speeds. The picture above is an S80 mid-impact in an offset "Elk test." | |
Of course, before any vehicles are crashed, Volvo will simulate hundreds of possible combinations using their Computer Aided Engineering (CAE) software. Thomas Broberg, Safety CAE Engineer, detailed the "Virtual part of (the) Volvo Safety Center," explaining that "before the physical development (of a Volvo), the CAE is brought in to simulate the vehicle's reactions to five possible accident scenarios: Front/offset, rear impact, side impact, rollover, and pedestrian." With the ability to run and re-run full-scale crashes, the CAE is used to calculate the human and vehicle's reactions to at different forces and angles.
Once the various elements of a vehicle have been individually tested and re-tested, then tested together and re-tested, the construction of a physical prototype is built and the set-up begins. While maximum capacity estimates that 200 vehicle crashes will be performed each year, the average set-up time for each accident is approximately one week --not including evaluations and lab time.
After the briefing, we were escorted into the massive testing room. Two long tunnels connect to a multi-level center that has an open and enclosed observation deck. Two tracks join together at a large glass-bottom floor that houses numerous high-speed cameras and lights.

As a demonstration of the new facilities capabilities, the Safety Center arranged a crash between their full-size S80 luxury sedan, traveling at 50 kilometers per hour, into their compact V40 wagon, traveling at 30 kilometers per hour at a 90-degree angle. With an average sized adult male and female in the front seats of the S80, and one adult male driving with another sitting in the rear right seat of the V40, they were scheduled for a T-bone accident. The S80 was programmed to hit the V70 directly where the driver and passenger are seated, between the A and C pillar, as though one of the vehicles were running a red light. We were shown the position of the accident with brightly colored demo cars that were rolled off as the group was split up and ushered to the observation decks.
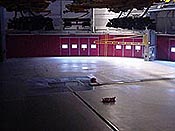
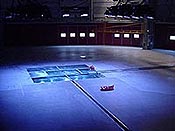
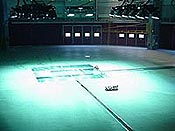
The process was mesmerizing and almost surreal. First, all of the lights were turned off. Then, the large block of 8,000-watt daylight photo lamps, suspended above the glass were slowly turned on and lowered from the ceiling. A total of 32 lights brighten the glass square that, going from a bright blue to an almost-blinding clear glow, the entire building was hollow and silent, except for a low hum.

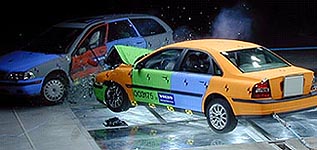

The crash itself was over within milliseconds. There was a click of engagement, the whir of them speeding up, the cars disengaged from their tracks and they collided. The metal crunched, glass shattered, and airbags deployed. It sounded painful and two oddly painted bodies were left awkwardly perched in their final resting position.

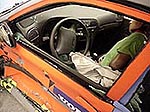

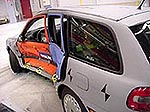
It wasn't a comfortable sight. The vehicles were mangled and the crash test dummies were left hanging in their seatbelts. Blue "lipstick" and green "mascara" marks were left on the S80's already deflated airbags, various windows were blown out, and body panels were buckled. The cars looked totaled.


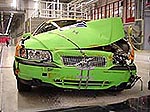

And it was all caught on tape. Thirty high-speed cameras simultaneously recorded every millisecond of the accident from above, alongside, and beneath the accident point. Capturing as many as 3000 frames per second, the film will be analyzed and compared to the data that was collected from the various sensors that were placed on each of the cars.
As a result of the new Safety Center…
Will safer, stronger, smarter cars be built? Absolutely. Will every accident prove survivable? No. Why? Because, regardless of how well a vehicle is built, materials and the human body are only able to withstand a certain amount of force, regardless of how many cushions there are to pad them. So, what will probably prove to be the best resource that the new Safety Center will produce? Knowledge. And with that knowledge, better reactive and proactive safety systems will be refined and invented, and more people will be saved from injury or death.